LCA shows 150 years of life cycle for Porotherm
Bengaluru, Nov 25, 2024 –
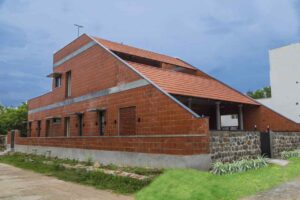
wienerberger India’s flagship product, Porotherm Smart Bricks, has demonstrated an exceptional environmental performance in a recent Life Cycle Analysis (LCA) conducted by LEAD Consultancy and Engineering Services (India) Pvt Ltd.The LCA, adopted the ‘Cradle to Grave’ approach, adhering to international standards (EN 15804+A2 & ISO 14025 / ISO 21930) and assessed the Global Warming Potential (GWP) of various walling materials. The ‘Cradle to Grave’ approach covers entire life cycle of a product from the excavation of raw materials to manufacturing process, transportation, installation, and usage to its end-of-life phases.
Porotherm Smart Bricks including Porotherm HP, Porotherm Plus, FB Exteria and Grinded bricks showed a remarkable GWP of 97.103 Kg CO2e per ton, significantly outperforming other materials. The lifespan of Porotherm is 150 years as per the LCA report.
Porotherm Vs other walling materials The Global Warming Potential (GWP) of Porotherm is much lesser as compared to other walling materials as per the LCA
– Porotherm: 97.103 Kg CO2e/ton
– Autoclaved Concrete: 230 Kg CO2e/ton
– Burnt Clay Bricks: 330 Kg CO2e/ton
– Concrete Blocks: 400 Kg CO2e/ton
– Reinforced Concrete Wall: 800 Kg CO2e/ton
For a typical 1500 Sqft residence, Porotherm’s total embodied carbon is 1491, compared to:
– 3172 for Autoclaved Concrete
– 21133 for Burnt Clay Bricks
– 18401 for Concrete Blocks
– 52277 for Reinforced Concrete Wall
“This significant reduction in carbon footprint underscores our commitment to sustainability,” said Mr. Monnanda Appaiah, Managing Director, wienerberger India. “Our eco-conscious approach enables us to create environmentally friendly products, contributing to a greener future.”
Sustainable Manufacturing
Porotherm’s composition includes an impressive 90% recycled waste, including:
– Stone slurry – Rice husk – Tank clay (silt removed from dead tanks and lakes during de-silting)
Only 10% of the raw material is clay sourced from clay mines. This innovative use of recycled materials significantly reduces waste and minimizes the product’s ecological footprint.
The benefits of Porotherm’s sustainable manufacturing process extend beyond environmental benefits, offering:
– Reduced waste disposal costs – Conservation of natural resources – Lower energy consumption